Advantages of Laser Cutting Equipment for Metal Fabricators
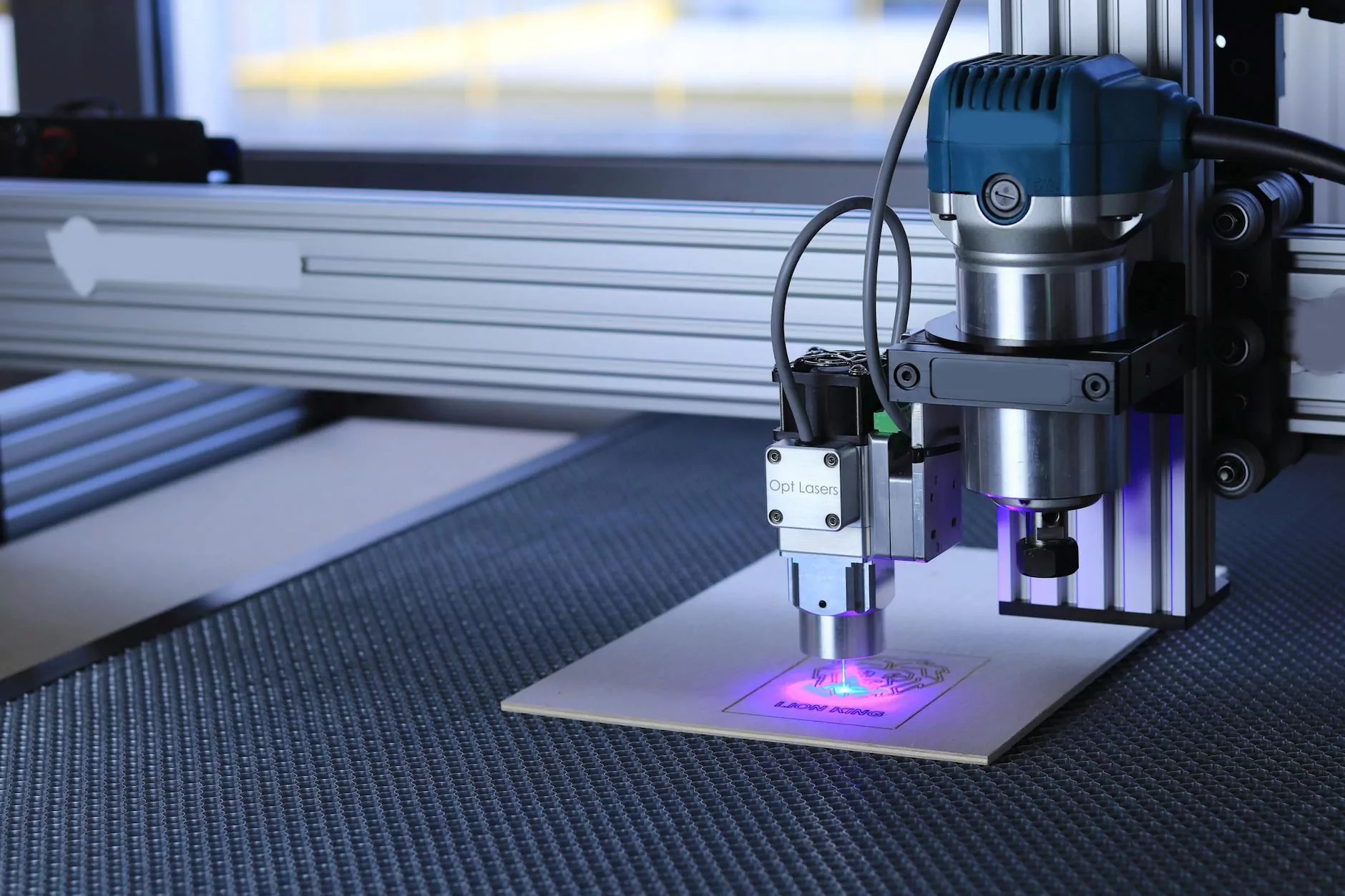
Introduction
In today's competitive business landscape, metal fabricators need cutting-edge technology to stay ahead. Laser cutting equipment has emerged as a game-changer, revolutionizing the metal fabrication industry. With its precision, efficiency, and vast capabilities, laser cutting has become an indispensable tool for metal fabricators worldwide. In this article, we will explore the numerous advantages of using laser cutting equipment, specifically for metal fabricators.
Precision and Accuracy
Laser cutting equipment offers unparalleled precision and accuracy, making it an ideal choice for metal fabricators. The focused laser beam can achieve incredibly small and intricate cuts with minimal material waste. The high level of precision allows for the creation of complex designs and patterns, ensuring exceptional quality and detail in the final product. Metal fabricators can produce parts with tight tolerances, meeting the most demanding specifications.
Efficiency and Productivity
One of the key advantages of laser cutting equipment is its efficiency, which directly translates into increased productivity. Laser cutting technology eliminates the need for time-consuming manual processes, such as marking guidelines or drilling pilot holes. With laser cutting, the entire cutting process can be automated, reducing production time significantly. This increased efficiency allows metal fabricators to handle larger workloads, meet tight deadlines, and ultimately enhance their overall productivity.
Versatility and Flexibility
Laser cutting equipment offers unparalleled versatility, allowing metal fabricators to work with various materials and thicknesses. Whether it's stainless steel, aluminum, copper, or even exotic alloys, lasers can cut through them all. This versatility extends to different shapes and sizes as well. Laser cutting machines can create intricate cuts, bevels, and curves, enabling fabricators to produce complex parts without the need for multiple tools or additional setups.
No Contact Cutting
Unlike traditional cutting methods that involve physical contact and mechanical force, laser cutting is a non-contact process. The laser beam melts, burns, or vaporizes the material, resulting in minimal heat-affected zones and negligible distortion. This non-contact cutting eliminates the chances of damage or deformation, ensuring the highest quality and accuracy in the final product. Additionally, the absence of physical contact means less wear and tear on the equipment, leading to reduced maintenance costs and increased longevity.
Speed and Cost-effectiveness
Laser cutting equipment is known for its impressive cutting speed, allowing metal fabricators to complete projects in a fraction of the time compared to traditional methods. The increased speed combined with the ability to process multiple parts simultaneously translates into significant cost savings for businesses. Laser cutting also minimizes material waste by optimizing part nesting, making it an environmentally friendly and cost-effective solution for metal fabricators.
Minimal Post-Processing
Another advantage of laser cutting equipment is its ability to produce finished parts with minimal post-processing requirements. The clean and precise cuts delivered by lasers often eliminate the need for additional finishing processes like deburring or sanding. This not only saves time and labor but also enhances the overall efficiency of the fabrication process. Metal fabricators can deliver high-quality products more quickly, providing a competitive edge in the market.
Conclusion
As technology continues to evolve, metal fabricators who embrace laser cutting equipment gain a valuable competitive advantage. The precision, efficiency, and versatility offered by laser cutting are a perfect fit for the demanding requirements of the metal fabrication industry. From intricate designs to cost savings and increased productivity, laser cutting has revolutionized the way metal fabricators operate. By adopting this advanced technology, businesses can stay ahead of the curve and secure their position in a highly competitive market.